京セラがサーマルプリントヘッドで培った技術についてご紹介します。
サーマルプリントヘッドで培った保有技術
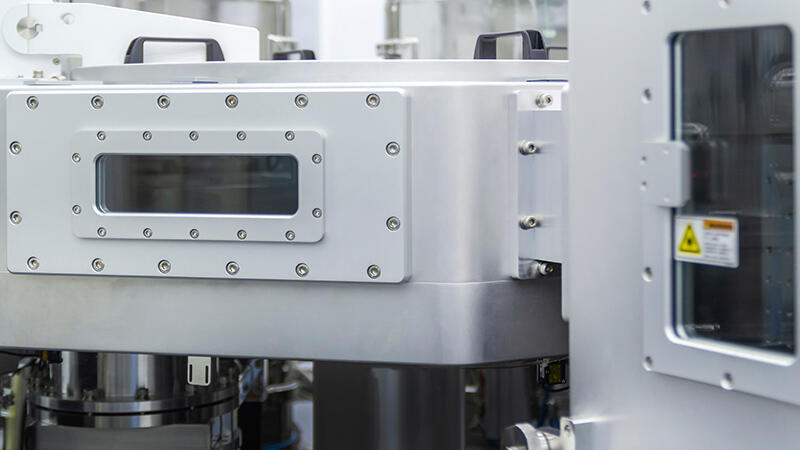
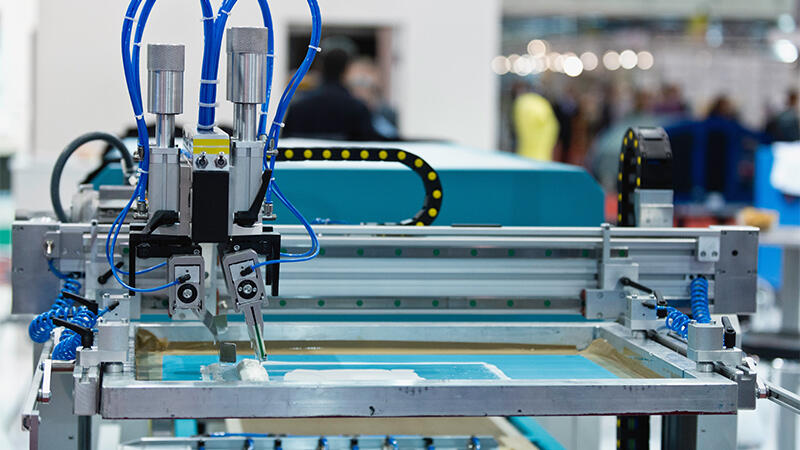
薄膜成膜技術
サーマルプリントヘッドで培った成膜技術で導電性材料から絶縁材料まで各種材料を数10nm~数μmの膜厚で成膜ができます。高い品質と求められる性能を最大限に引き出すため、様々な成膜手法を採用しています。また、量産可能な生産環境を保有しています。
【実用例】抵抗膜/電極膜/保護膜の成膜
スクリーン印刷技術
サーマルプリントヘッドで培ったスクリーン印刷技術で導電性材料から絶縁性材料を数10μmの膜厚で形成することができます。印刷技術とともに高い品質と求められる性能が得られる材料選定から対応しています。また、量産可能な生産環境を保有しています。
【実用例】パターン/保護層の印刷形成
フォトリソグラフィ技術
サーマルプリントヘッドで培ったフォトリソグラフィ技術で抵抗膜、電極膜など導電性材料の薄膜を数μmのライン&スペースで配線形成することができます。高い配線形成精度により高い品質と安定した性能を確保することが可能です。また、量産可能な生産環境を保有しています。
【実用例】発熱体(ヒーター)/パターンの形成
めっき形成技術
サーマルプリントヘッドで培っためっき形成技術で金属電極上に数μmの膜厚でめっきを形成することができます。複雑なパターン形状にも形成でき、均一なめっき厚を形成することが可能です。さらに、優れたはんだ付け性により完成品の高い信頼性を実現しています。また、量産可能な生産環境を保有しています。
【実用例】ドライバIC/電装部品接合用めっき形成
アッセンブル技術
サーマルプリントヘッドで培った実装技術で高密度フリップチップを数10μmの搭載精度でドライバICを実装することができます。また、ドライバICのフリップチップ実装用はんだバンプ形成技術も保有しております。その他、フレキシブル基板(FPC)とセラミックス基板接合技術などのアッセンブル技術も保有しており、国内外に量産可能な生産環境を保有しています。
【実用例】ドライバIC·電装品の実装/接合、フリップチップ用はんだバンプの形成
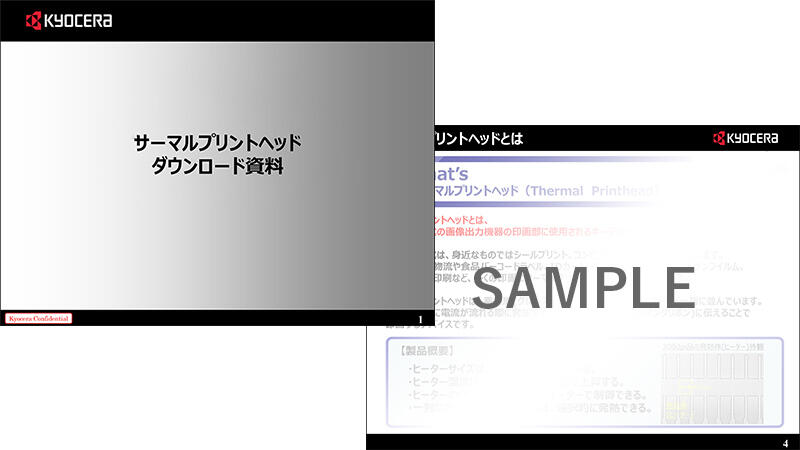