京セラが半導体ウエハ後工程を
受託する理由
~事業化の経緯~
なぜ京セラが半導体製造受託事業を?
京セラは、UBMめっき/はんだバンプ加工などの半導体ウエハ後工程受託サービスを提供しています。
しかし、半導体業界内での認知度は高くありません。
ファインセラミックス領域の事業を祖業とする京セラにとって、
本サービスは一見すると関係なさそうに思えますが、実は深い関わりがあります。
本ページでは「なぜ京セラが半導体製造受託サービスを提供しているのか?」について、
関連事業の歴史とひもづけて解説いたします。
サーマルプリントヘッドの
開発/立ち上げ
1970年代後半、京セラでは、「来たる情報通信時代において、ファクシミリが普及する」として、当時主流であったインパクトプリンター方式よりも静音性や省メンテナンス性に優れるサーマルプリント方式に着目し、その印画部に使用されるサーマルプリントヘッドの開発をスタートさせました。当時は、業務用ファクシミリ用途でサーマルプリントヘッドが普及しつつあった時代であり、京セラは後発メーカーでありましたが、先行メーカーが採用していた厚膜方式ではなく、薄膜電極形成技術を応用した薄膜方式サーマルプリントヘッドの開発を進めました。
そして、1983年よりサーマルプリントヘッドの量産を開始。それまでのダイオード搭載サーマルプリントヘッドに代わり、新たにドライバIC搭載サーマルプリントヘッドの生産を立ち上げました。ICと基板はワイヤーボンディングで接続させる仕様でした。
しかし、硬いセラミック基板の上に薄く形成されたAu電極に金線をボンディングすると、金線が電極に付かない事態が頻発。電極のめっき条件などを工夫することで生産性を改善し、なんとか量産工程を立ち上げました。めっき技術の蓄積が、半導体ウエハ後工程受託サービス立ち上げに貢献することになります。
サーマルプリントヘッド
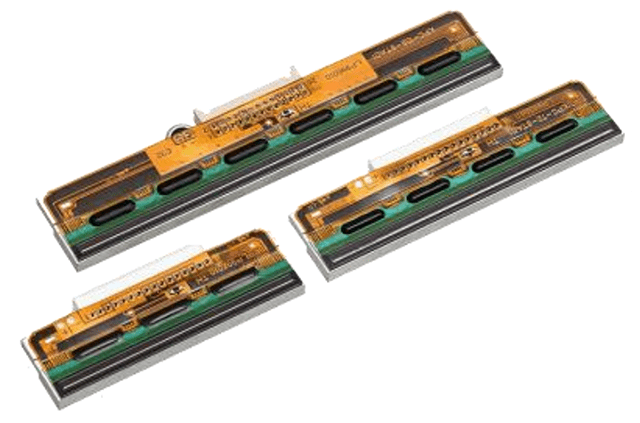
ワイヤーボンディング実装方式
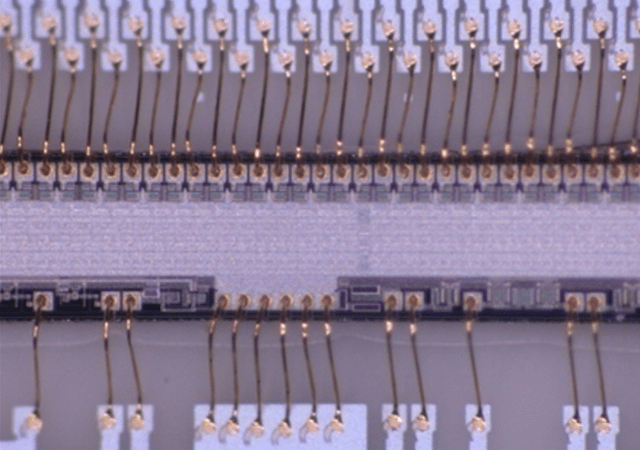
一早くフリップチップ実装を採用
80年代中盤から後半にかけて、ファクシミリ需要が急激に伸び、ファクシミリ市場の成長とともにサーマルプリントヘッドの生産量も拡大していきました。そんな中、1985年に京セラはサーマルプリントヘッドのドライバIC実装方式を、従来のワイヤーボンディング実装方式からフリップチップ実装方式へ切り替えました。立ち上げ当初から問題であったワイヤーボンディング時の金線断線問題を解消しきれず、まだまだ生産歩留まりが不安定であったためです。
ただし、フリップチップ実装方式を採用するためには、ICウエハ生産工程をICメーカーと共に一から開発する必要がありました。また京セラにおいても、セラミック基板上へのめっき処理に関するコア技術開発が必要でしたが、めっき処理条件の最適化検討を繰り返すことで、フリップチップ実装への切り替えに見事成功し、工数削減と信頼性向上を同時に達成することで、飛躍的な生産性の向上を実現しました。
今でもワイヤーボンディング実装方式を採用するサーマルプリントヘッドメーカーが多く、当時としても相当な技術的ハードルでありました。1990年代以降、一部の業務用コンピュータ以外にも徐々に普及していくフリップチップ実装方式ですが、京セラはすでに1980年代からサーマルプリントヘッドにて量産採用していました。
フリップチップ実装方式
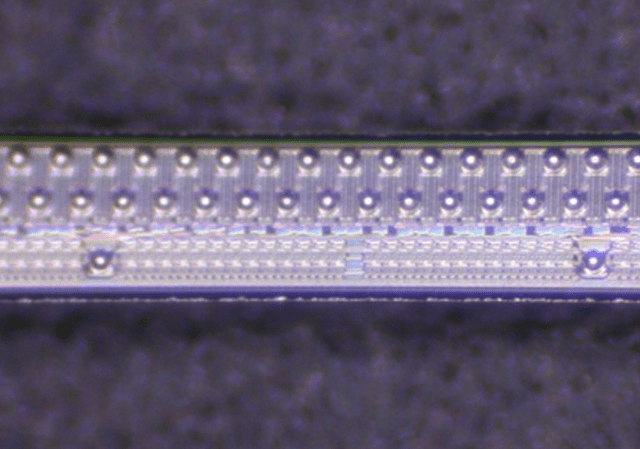
ドライバIC用ウエハ
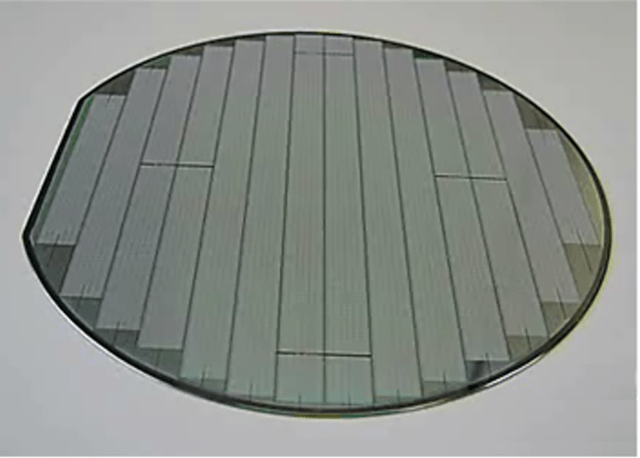
UBMめっき/はんだバンプ加工工程の
内製化に成功
1998年~99年頃、液晶ディスプレイの需要が急増しました。そして液晶用ICの供給が優先された結果、サーマルプリントヘッドのドライバICメーカー様より「はんだバンプ付きICの供給をやめたい」という打診を受けた京セラは、液晶ディスプレイの需要がさらに伸び続ける可能性を考慮し、UBMめっき/はんだバンプ加工工程の内部取り込み(内製化)を決断しました。
これまでサーマルプリントヘッドの市場成長をけん引してきたファクシミリ用途に加え、バーコード印刷用途やPOS(レシート)印刷用途など、当時のサーマルプリントヘッドの市場規模/使用用途は拡大していました。それに対応しながら内製化させなくてはならず、課題の多いプロジェクトでした。
技術的には、ウエハUBMめっきに関する課題が大きく、特にAl電極端子の酸化膜を除去してからすぐにNiメッキをのせる技術は、当時世界でも数社しか確立していない技術でした。これに対し京セラは、それまでのサーマルプリントヘッド製造工程で培った技術をベースに、独自の無電解めっき加工プロセスと、めっき装置の開発に成功しました。
これが、半導体ウエハ後工程受託サービスのベースとなりました。
ドライバIC用ウエハ(拡大)
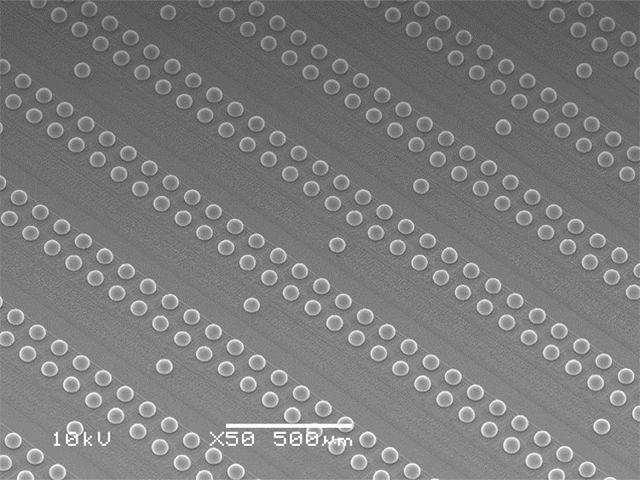
はんだバンプ(拡大)
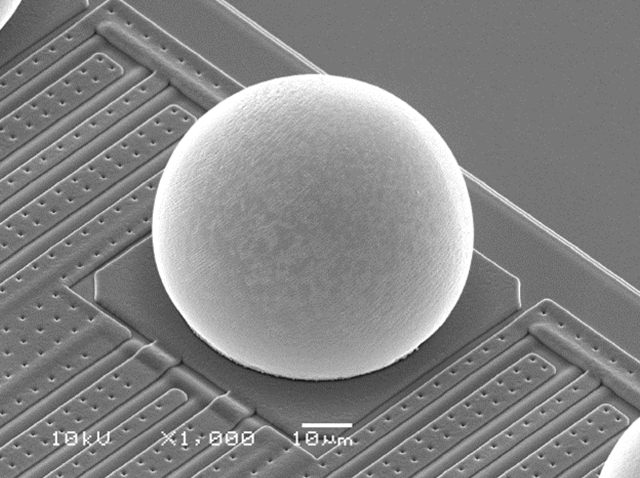
半導体ウエハ後工程
受託サービスを事業化
2000年代に入ると、電子機器の小型・高機能化がより一層加速し、小型/薄型のICが求められるようになりました。京セラは、サーマルプリントヘッドのIC実装で確立したUBMめっき/はんだバンプ加工の品質で社会に貢献したいと考え、2007年に半導体ウエハ後工程受託サービスを事業化しました。
半導体業界の右も左もわからない状況で営業活動をスタートさせましたが、腕時計用ICでの採用を皮切りに、今では、スマートフォン、デジタルカメラ、自動車、各種産業用機器に搭載されるICの後工程をご依頼いただいています。
半導体ICの高集積化はこれからも進んでいき、小型/薄型化が進んでいくと考えられています。京セラは、半導体ウエハ後工程受託サービスを通して、日本の半導体業界の発展に貢献していきます。
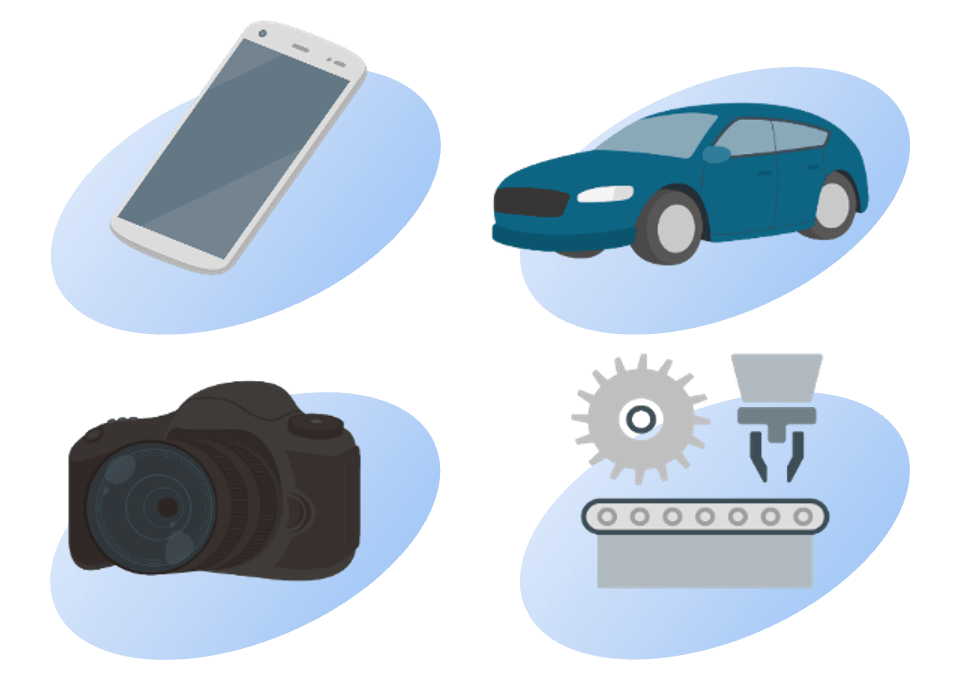
まとめ
本ページでは、京セラの半導体ウエハ後工程受託サービス事業の沿革をご紹介しました。
京セラは、UBMめっき/はんだバンプ加工を含む半導体ウエハ後工程受託サービスを提供しております。
ご不明点がございましたら、何でもお気軽にお問い合わせください。
下記リンク先にてサービス紹介カタログもダウンロードできますので
ぜひお客様における半導体デバイスの調達戦略構築にお役立てください。
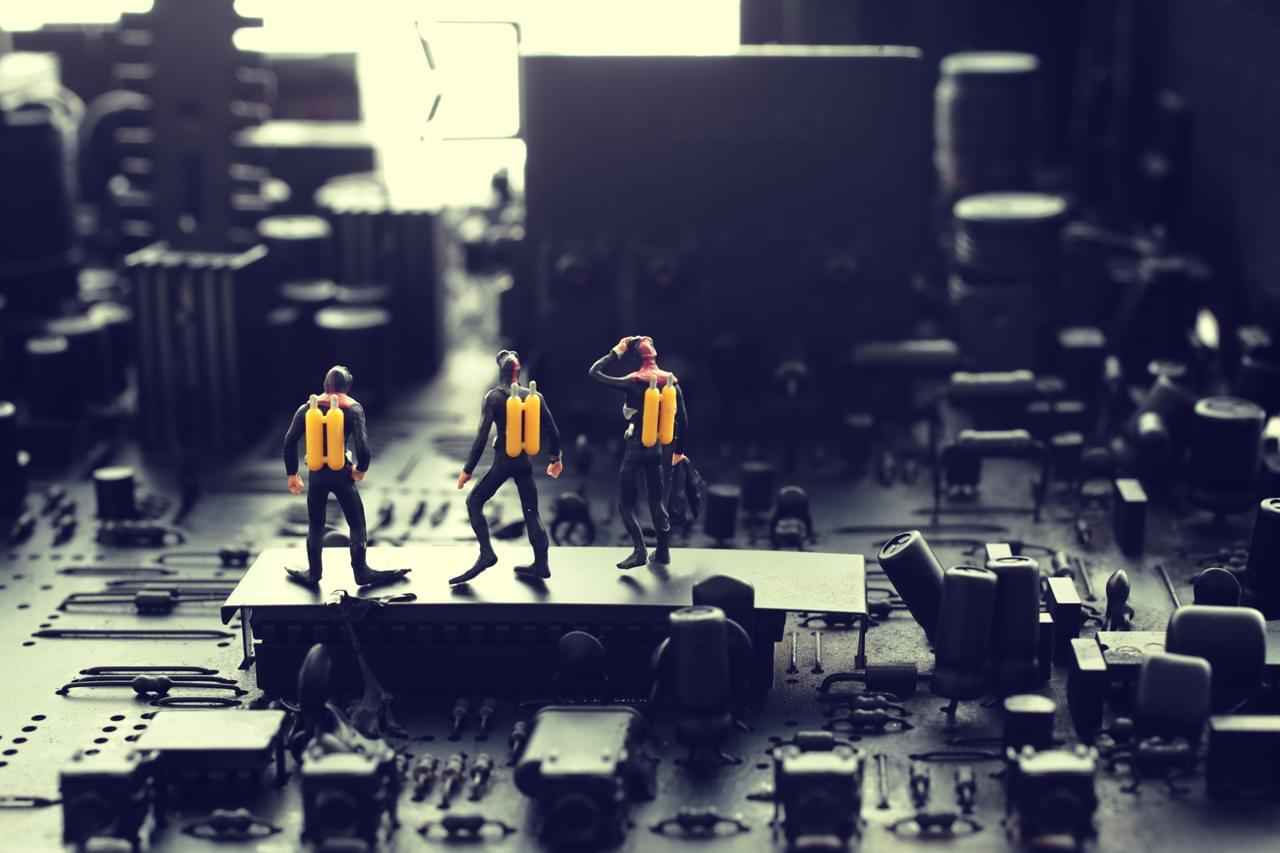